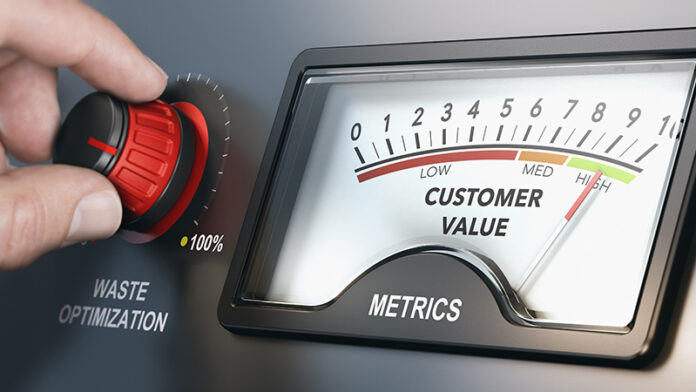
El Lean Manufacturing o manufactura esbelta, es una filosofía de gestión que tiene sus raíces en la evolución histórica de la producción industrial, desde la Revolución Industrial hasta el desarrollo del Sistema de Producción Toyota. Su enfoque se basa en maximizar la eficiencia y la calidad mientras se minimizan los desperdicios en todos los procesos de la empresa.
Evolución histórica de la manufactura
La manufactura ha evolucionado significativamente desde la Revolución Industrial. James Watt, con su máquina de vapor, sentó las bases de la industrialización en 1776. Eli Whitney, en 1798, introdujo las piezas intercambiables, lo que permitió la estandarización de la producción. A principios del siglo XX, Henry Ford mejoró la eficiencia al implementar la línea de ensamblaje en 1913, lo que optimizó la producción masiva con especialización en tareas.
Sin embargo, el Sistema de Producción Toyota (TPS) consolidó los principios que ahora son fundamentales en el Lean Manufacturing. Creado por Sakichi Toyoda, el TPS introdujo el concepto de jidoka que es la automatización con enfoque humano, y el sistema Just in Time (JIT). Estos principios transformaron la industria al permitir que los procesos de producción fueran más flexibles, adaptándose mejor a las demandas del mercado.
El Toyota Production System (TPS), concebido en las décadas de 1950 y 1960 por Taiichi Ohno y otros ingenieros de Toyota, revolucionó la fabricación al enfocarse en la eliminación de desperdicios, la mejora continua (kaizen), y la producción justo a tiempo (JIT). En Japón, estas prácticas ayudaron a Toyota a convertirse en una de las empresas automotrices más eficientes y competitivas del mundo, pero su impacto no se extendió globalmente en un principio.
El Toyota Production System (TPS), desarrollado por la compañía automotriz Toyota, era un secreto bien guardado en Japón. Fue durante los estudios del Programa Internacional de Investigación de Vehículos Motorizados (IMVP) del Massachusetts Institute of Technology (MIT), liderados por James P. Womack, que el TPS fue documentado y analizado de manera sistemática. Estos estudios llevaron a la publicación del libro «La máquina que cambió el mundo» en 1990, donde Womack y su equipo describieron detalladamente el TPS y lo rebautizaron como Lean Manufacturing. La difusión de los principios Lean a través de este libro y los esfuerzos posteriores de Womack y el Lean Enterprise Institute (LEI) hicieron que el TPS o LEAN se conociera y adoptara ampliamente en muchas industrias fuera de Japón.
Taiichi Ohno y Shigeo Shingo, también implementaron herramientas como el poka-yoke que son los dispositivos a prueba de errores y el SMED para el cambio rápido de herramientas con el fin de reducir los tiempos muertos y optimizar el uso de los recursos.
Principios clave de Lean Manufacturing
El Lean Manufacturing se enfoca en cinco principios fundamentales que ayudan a las empresas a ser más competitivas y eficientes:
- Eliminación de desperdicios: Este principio aboga por identificar y eliminar actividades que no agregan valor, como la espera, la sobreproducción y los transportes innecesarios.
- Calidad en el origen: Garantizar que la calidad se logre desde el principio del proceso, no al final. Esto implica inspeccionar y prevenir defectos durante la producción.
- Participación del personal: Involucrar a todos los empleados en el proceso de mejora continua. Esto se logra mediante la capacitación y el uso de herramientas visuales que faciliten la toma de decisiones.
- Adaptabilidad y eficiencia: Las empresas deben ser capaces de adaptarse rápidamente a los cambios en la demanda sin sacrificar la calidad ni la rentabilidad.
- Mejora continua: La cultura Lean promueve una constante búsqueda de la optimización en todos los niveles de la empresa, mejorando procesos y reduciendo los costos de manera sostenida.
Aplicaciones de Lean Manufacturing
Lean Manufacturing no se limita únicamente a la manufactura. Con el tiempo, los principios del TPS se han extendido a otros sectores como la salud con el Lean Healthcare, la administración pública con Lean Government, la logística con Lean Logistics y el diseño con Lean Design. Esta flexibilidad demuestra cómo Lean puede ser aplicado para mejorar la eficiencia y reducir desperdicios en una amplia gama de industrias.
Es así que ell método Lean ganó gran notoriedad después de la crisis del petróleo de 1973, cuando Toyota demostró que, aplicando estos principios, podía ser más rentable y productiva que sus competidores, incluso en tiempos de escasez de recursos. Su éxito inspiró a empresas de todo el mundo a adoptar el Lean Manufacturing para mejorar sus procesos, reducir costos y responder de manera más ágil a las necesidades del cliente.
La clave para implementar Lean de manera efectiva radica en la participación de los empleados y en una cultura organizacional sólida. La capacitación continua y el liderazgo efectivo son fundamentales para motivar al personal y asegurar que las herramientas Lean sean aplicadas correctamente.
Lean en acción: Ejemplo práctico de JIT y Kanban
El Just in Time, JIT, y el sistema Kanban son herramientas clave dentro de Lean. JIT asegura que los productos se fabriquen solo cuando son necesarios, evitando sobreproducción y optimizando el inventario. En una fábrica textil, por ejemplo, el uso de Takt time permite ajustar la producción al ritmo de la demanda del cliente.
El sistema Kanban, mediante tarjetas visuales, regula la producción en función de la demanda real, lo que optimiza el flujo de trabajo y asegura que no haya interrupciones en la cadena de producción.
Si deseas profundizar en cómo aplicar Lean Manufacturingy aprender las herramientas necesarias para lograr mejoras tangibles, te invitamos al evento virtual «Conoce cómo mejorar la producción de una empresa: Lean Manufacturing». En este evento, aprenderás:
- Herramientas Lean
- Uso e implementación de Lean Manufacturing paso a paso
- Lean Manufacturing para equipos de trabajo y pensamiento Lean
Fecha: 16 de enero a las 7:00 pm
Plataforma: Zoom
Evento realizado por: Carrera de Ingeniería Industrial de la modalidad a distancia de la Universidad Continental, con opción a doble título estadounidense con CFU.
Participación especial de: Continental Florida University.
"*" señala los campos obligatorios
